Next-generation, software-defined devices deliver business benefits for OEMs and end-users
Multiapplication devices deliver operational benefits for OEMs while future-proofing electrical systems to help industrial customers reach their operational and sustainability goals.
OEMs play a crucial role in ensuring customer success by designing systems that help lower costs, increase efficiencies, and promote customer adaptability to changes in the power industry. Software-defined, multiapplication devices help OEMs deliver solutions that meet their customers’ needs while providing operational benefits for themselves.
Protection relays are one of the best examples of multiapplication devices designed to deliver substantial benefits to both end-user and OEM. These relays safeguard critical equipment such as motors, transformers, and generators by detecting electrical faults and disturbances. When an event happens, the relay sends a signal to a circuit breaker through an FT switch before the fault can lead to equipment damage, system downtime, or safety hazards.
The traditional approach to protection and control of distribution switchgear requires using a separate protection relay type for feeder, transformer, busbar, main incomer, etc. Now, a newer generation of protective relays is emerging in which multiple applications can be combined into one device. This type of device is software-defined and uses the same tools for the configuration and operation of its functions as the previous generator of devices.
Reduce inventory handling and decrease lead times
As simple as the concept of a protection relay is, every customer project is unique. Each model of the traditional protection relay can have hundreds of variants, leading to a proliferation of SKUs. Instead of tying up working capital and warehouse space, OEMs have typically opted to custom-order relays for each project.
Unfortunately, this custom approach lengthens lead times. Multiple SKUs can even create more “weak links” in the supply chain, making the OEM’s business vulnerable to supply chain disruptions. Work stoppage anywhere along the chain can delay shipments for weeks if not months. Major events, like a global pandemic, can have even longer lasting ramifications. Since OEMs deal directly with the customer, they often feel the heat when shipments are delayed.
For OEMs, software-defined configurability dramatically reduces the need to spec, order, and stock multiple SKUs. In an industrial setting, basic applications such as feeder, motor, and voltage protection account for 80% or more of the customer needs. These needs can be addressed through the software configuration of products like the ABB REX610.
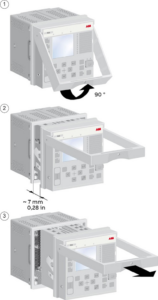
Decrease maintenance requirements and extend equipment life
Software-defined devices make installation faster and maintenance easier as technicians only need to learn how to wire one unit. Furthermore, the plug-in units can be easily removed from the chassis during maintenance, delivering a MTTR (Mean time to Repair) of less than 15 minutes.
Moreover, a software-driven approach allows these relays to collect electrical disturbance data for centralized/virtualized applications that provide fault prediction and condition-based maintenance. For instance, reliability standards mandate periodic testing of circuit breakers, with higher-than-expected travel times indicating the need for maintenance of the circuit breaker mechanisms. The ABB family of multiapplication relays lower costs by monitoring travel time, allowing for a correction factor to be applied through software controls. The remaining life of the breaker can also be estimated by programming the breaker trip curve.
Additionally, the ability to collect data helps end-users monitor systems installed in harsh or variable environmental conditions. In an industrial substation, grounding switches and disconnectors are often located outside. Mechanical actuation of switches is affected by exposure to varying weather and environmental conditions. Multiapplication relays monitor circuit breakers and switches to assess their mechanical condition and alert operations to when maintenance may be needed.
Enable customer adaptability and sustainability goals
Power reliability is a critical goal for the OEM’s customer as it is essential to ensuring uptime and delivering on customer commitments and service level agreements. However, the dynamics of power consumption have changed, with many industrial customers having goals such as increasing efficiencies and the use of renewable sources for a lower carbon footprint. Technologies like AI and Machine Learning are also featuring prominently in many strategy planning documents.
Ever-more complex power distribution systems and changing end-user goals require the kind of flexibility that modular, multiapplication devices provide. For example, during the design stage of a project, if incident energy during arc fault is higher than anticipated levels, and the protection scheme needs to be changed from Zone Selective Interlocking (ZSI) to differential protection as per NFPA 70E, multiapplication relays can easily be modified due to their modular design. Additionally, if power quality needs to be measured for critical electrical processes, a mere software update in multiapplication relays would suffice.
Finally, multiapplication relays are a great way to help end-users extend the benefits of AI and Machine Learning to their power consumption and operational goals. This data can be used by powerful analytical systems to provide deeper insights into opportunities to meet sustainability goals.
Future proofing your business and your customers
Software-defined, multiapplication devices represent a shift towards more flexible, efficient, and adaptable technology solutions. By leveraging software for configuration and operation, they offer significant benefits over traditional hardware-centric approaches, including reduced inventory management requirements and increased adaptability to change. A software-driven approach also allows end-users to leverage anomaly data to train neural network models for various machine learning applications that help them reach sustainability goals and improve operational performance.
See related blog post “Enhanced circuit protection: An evolution in safety, efficiency, and reliability”
—
Vivek Singh, P.E. PMP
Manager, Marketing & Business Development
Dinesh Baradi
Technical Specialist – Digital Substation Products
Jesse Koskela
Product Marketing Specialist – Digital Substation Products