Are you selecting and installing your rope-pull safety switches correctly?
Rope-pull safety switches remain a simple but effective approach to providing safety stops along conveyors and in other applications. Despite their simplicity, care is required to ensure these systems are designed and installed correctly.
Digitalization and the internet of things have driven some remarkable advances in machine-safety technology. But there are some applications where the way we’ve done it for decades remains the best way. One example is the rope-pull (a.k.a., cable-pull) safety switch. This basic device is often the right choice to protect people and equipment.
While the concept is simple, there are still many ways that these systems can be designed or installed incorrectly, increasing the risk of personal injury, down time, and machine damage. The following are the essential things you need to know to correctly specify, deploy, and maintain a rope-pull safety switch system.
The basics
A “wire” or cable is located along a conveyor so that an operator can trip the safety switch by pulling the cable regardless of where they are standing along the protected side of a conveyor. This approach is a huge cost savings compared to locating emergency stop buttons at regular intervals along the conveyor. A single rope-pull switch can provide the same level of protection as dozens of emergency stops. This approach creates significant upfront savings and reduces ongoing maintenance costs.
In most cases, a single rope-pull switch can do the job, with one end of the rope attached to the switch and the other to a spring anchored to a wall, frame, or other fixed attachment point (see figure 01 below).

For longer runs, typically above 100 meters, a second switch is recommended, one at each end. This arrangement overcomes the problem of maintaining proper rope tension in the system (see figure 02 below).

For very long runs of approximately 125 meters or more, multiple double rope-pull switches with rope connections in two directions are available. This is another cost-savings feature of these switches. One double switch can be used instead of two single switches (see figure 03 below).

Select the right components
Rope-pull switches are widely available from any number of manufacturers and suppliers. While the basic function is the same, the construction and materials vary. Low-cost foreign-made devices are
widely available but are typically a classic example of “you get what you pay for.” Where reliable safety and low maintenance are important, you need to choose wisely.
Another important consideration is tension monitoring to detect when the cable has stretched, broken, or pulled on. This can be accomplished using a tension-viewing window and local reset. The viewing window simplifies setting the proper tension. The local reset enables returning the system state to ready-to-run.
Also look at the construction of the switch body. The thickness and quality of the metal are major concerns for sustainability. For wet or corrosive environments, opt for switches with a stainless-steel body. Another consideration for wet or corrosive environments is an appropriate gasket between the switch body and its cover. An inadequate gasket will deteriorate over time, causing loss of IP rating and requiring switch replacement.
Set up the system correctly
A basic rope-pull switch system can be set up by anyone with the ability to read and follow instructions, but there are some common mistakes to avoid.
From the rope-pull switch to the first cable guide, the rope must remain in a straight line. Rope should not be installed at an angle from the switch to the first eyelet. This affects its performance and increases the possibility of damaging the switch.
For straight runs, a good rule of thumb is that cable guides be equally spaced every three meters, but consult the manufacturers specification when possible. Even spacing is important to ensure reliable switch operation.
At any turns or bends, add corner pulleys. In most applications, a simple rope-pull switch pulley is adequate. However, these pulleys sometimes fail to operate correctly because the rope jumps out of the groove and may wedge between the pulley and the frame.
Some specialized corner pulleys have rollers surrounding the cable that eliminate the jamming that occurs with traditional corner pulleys. In addition, these roller guides can be used in bends less than 90 degrees.
In applications with long cable lengths and where large temperature changes can occur that could
expand or contract the cable, you may need to regularly readjust the tension. Otherwise, you could experience unnecessary machine stops.
You must use the proper cable for the system. This might seem obvious, but there are installations where clothesline was used as the cable. Steel cable provided by the manufacturer of the rope-pull switches is highly recommended, and it is required that the cable be red, not blue or green.
Consider added features
Rope-pull switches are available that include a status LED on the side that indicates the switch is ready (green) or has been tripped (red). This is beneficial in longer rope runs that require several switches. The LED enables at-a-glance identification of where the stop was initiated and needs to be reset from. It’s also possible to incorporate stack lights to further speed and simplify the process of identifying the trip location.
Also stack lights and horns can be used to indicate the starting or stopping of a conveyor system. Think about the last time you were waiting on your luggage at the airport and the horn started along with lights before the conveyor moved.
Some manufacturers offer thimbles and clamps to attach the cable both to the switch and to the spring. Attaching them can be a tedious process that leaves you wishing for a third hand. Also, over time the cable tends to slide between the clamps. To solve this problem, some suppliers offer tensioners that use built in cable-clamping mechanisms that eliminate the need for thimbles and clamps while securely fastening the cable.
While adjusting the cable tension, a handy feature is the easy-to-read viewing window mentioned earlier, which is available from some suppliers to simplify setting and monitoring cable tension (see figure 04 below). The combination of the viewing window and the tensioner makes installation and maintenance of your rope-pull system easier and faster.
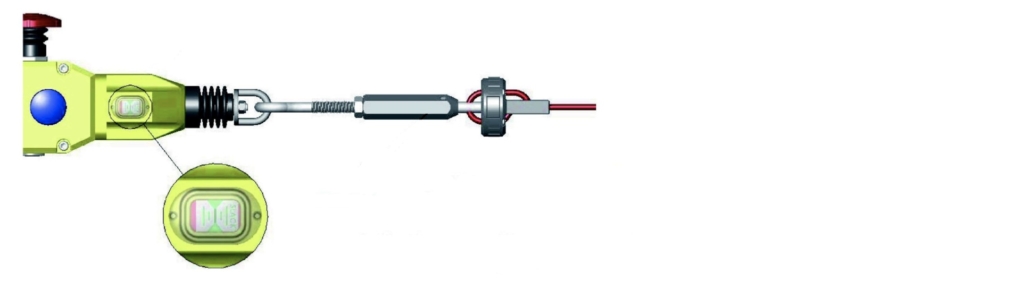
A final special feature is an estop button on some switches that allow operators to initiate a stop if they are standing near the inactive zone between the switch and the first cable guide. This is especially important with a two-way rope-pull switch since the inactive zone is much larger. Some rope-pull switches allow the addition of this emergency stop to the switch body itself.
Smart choices for rope-pull switches
New technology is great, but not always an improvement over simpler, proven approaches to safety. Rope-pull safety switches today do incorporate some sophisticated features, but the basics remain the same. These systems continue to be an excellent approach to providing safety stops on conveyors and in other applications.
You are probably operating today with a larger percent of your workforce lacking manufacturing experience and awareness of good safety practices. The simplicity of the rope-pull switch provides a way to ensure that your operators can quickly shutdown a conveyor or process.
While these switches are simple, it’s vital to select the appropriate components and install them correctly. Doing so ensures a high level of safety for both your operators and your equipment.
For more on machine safety, be sure to check out our article on the 4 Benefits of Safety PLCs.
—
Darrell Burkeen
Certified Machinery Safety Expert (TÜV Nord)
Jeffrey Leslie
Certified Machinery Safety Expert (TÜV Nord)