Selecting the right motor starter option
Of the various motor starter options, which is the best fit for your application? This article introduces the benefits and tradeoffs of the three main starter types: across-the-line starters, softstarters, and variable frequency drives.
The diversity of equipment in manufacturing and processing facilities is remarkable, but there is one device common to every industrial facility regardless of the product made, the scale of production, or location of the facility. Wherever there is motion in a facility, it is almost certainly propelled by an electric motor.
There are many ways to control power to those motors. Small, simple motors may require nothing more than an ON/OFF switch. As the size of the motor and the application complexity increase, plant engineers typically include a more advanced motor control device. This may be to protect the motor and application, provide higher levels of control, or to integrate it with an automation system.
This article explores the three most frequently used devices – across-the-line, softstarters, and variable frequency drives (VFDs) – including the pros and cons of each and criteria to help plant engineers select the appropriate device for each application.
Across-the-line starters
These devices, also known as direct-on-line, are the most basic and commonly used type of motor starters.
They simply connect and disconnect power to the motor, immediately applying full voltage, current, and torque. They are either ON or OFF, making them by far the easiest to install and operate and adding little complexity to the system. Compared to other motor starters, they require a low initial investment, making them cost-efficient in the short run.
Across-the-line motor starters can be used in any applications where the motor runs at a full speed. However, depending on the motor size and power supply, this starter type can draw a substantial current and create a voltage dip.
“Across-the-line starters are the most energy efficient of the starting solutions and can get almost any motor up to speed quickly, but they can also have significant drawback when controlling larger sized motors,” says ABB Global Product Manager Joakim Jansson. “When switched on, they can allow the motor to experience inrush currents as high as seven times greater than running current. This puts increased stress on the electrical system, possibly creating power fluctuations that may trip breakers or cause problems for other devices sharing the same circuit.
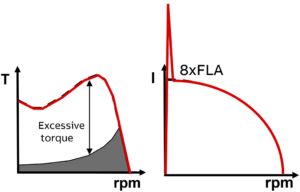
“They also allow many times higher motor torque than required during start. That can put significant and unnecessary mechanical stresses on the motor, couplings, bearings, and the mechanical equipment, possibly shortening equipment life.”
The excessive torque can be seen in figure 1 as the difference between the load torque (gray area) and applied torque from the motor (the red line). Starting the motor requires applied torque greater than the load torque. The larger the difference between the two, the greater the stress.
Softstarters
As the name implies, these devices provide a soft start by ramping up the speed of the motor. The softstarter controls the three-phase motor’s voltage supply as power is applied, adjusting the motor to the connected machine’s load behavior. The smooth acceleration reduces the electrodynamic stresses on the motor, power supply, and cables, largely eliminating excessive mechanical stresses on the motor, attached device, and drivetrain components. The reduced stress is visualized in figure 2.
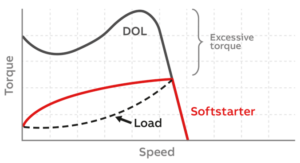
Softstarters provide the same benefits when stopping the motor.
“However, like the across-the-line starter, the softstarter provides no continuous, variable-speed control,” says Jansson. “While it brings the motor up to full speed more gently, it typically operates only at full speed. Softstarters are commonly used in applications driven by motors that operate at full speed and cycle frequently, like pumps, fans, compressors, and conveyors.”
When it comes to motor starting, softstarters provide many of the same features and benefits of the variable-frequency drive, including the ability to be integrated into facility or process automation systems. However, compared to VFDs, softstarters are smaller, lighter, and less complex, making them easier to install, control, and maintain.
Variable frequency drives
These are the most capable of the three devices, providing not only the ramping up and down of motor speed but also active motor-speed control. The major differentiator between VFDs devices and softstarters is that VFDs can provide sustained speed and pressure control.
The ability to reduce power to the motor and the motor speed also adds the benefit of energy conservation. While softstarter-connected devices run at constant, full-power load, VFD-connected devices can run at reduced loads, which in turn reduces energy consumption.
They can deliver full, rated current and torque as the motor starts from zero speed, a feature unique to VFDs. They do so without increased current draw while starting, making them well suited for applications with high starting torque.
“VFDs, like softstarters, can be fully integrated with building and process control systems, providing continuous motor-data feedback of speed, torque, and power,” explains Jansson. “The VFDs have an immense range of added features and complex algorithms for any kind of motor control. The ability to vary motor speed supports additional functions like loop set-point control to maintain constant process flows or pressures.
“Of the three, it’s not surprising that VFDs require the highest investment, but the potential long-term savings can also be substantial. A total-cost-of-ownership analysis and ROI calculation are required to determine if the investment makes sense.”
To take advantage of the many VFD features, the complexity of the device often requires experienced engineers for set up. In addition to the device cost, it may also be necessary to invest in filters to overcome the potentially harmful harmonics generated by the drives. VFDs also generate the most heat of the three options, incurring additional costs for cooling.
Making the choice
“The first decision point is whether variable speed is required,” says Jansson. “If so, then the VFD is the only choice. In applications that operate at constant full speed, the softstarter provides most of the benefits of a VFD. Of the hundreds of millions of electrical motors installed worldwide, the vast majority are used in full-speed applications. Considering that VFDs are larger, heavier, and typically cost two to three times as much as softstarters – and sometimes significantly more than that – softstarters are typically the best choice in these applications.”
For basic motor starting in applications where starts/ stops are infrequent, the across-the-line starter is the low-cost, small-size solution.
Of course, there are many additional device variables and application requirements to consider. Still, these fundamental motor-control device characteristics provide a good foundation for your selection process.
—
Joakim Jansson
Global Product Manager – Softstarters
ABB Electrification Business